Forbo's linoleum een duurzame vloer
Marmoleum is van nature duurzaam. Het vangt meer klimaatschadelijke CO2 op dan het uitstoot, als je het op de juiste manier produceert, zoals Forbo dat doet.
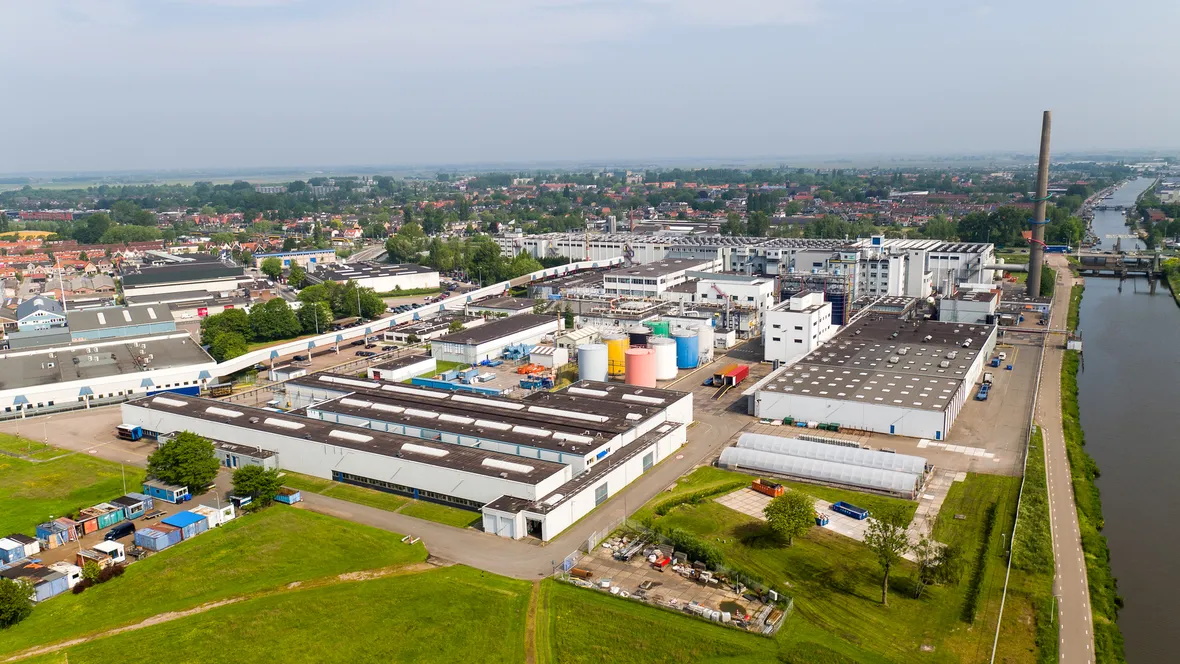
Wie vanuit Amsterdam richting Alkmaar rijdt, ziet vooral weilanden en grachten. Dit maakt de kleurrijke ringen rond de niet meer gebruikte schoorsteen van de fabriek bij de afrit van de Assendelft-autosnelweg des te opvallender. Het is echt een herkenningspunt', zegt Bregje Smulders. Ook al is het eigenlijk nooit gebruikt. De linoleumfabriek, de grootste en modernste linoleumfabriek ter wereld, op iets minder dan een half uur rijden ten noordwesten van Amsterdam, is de plaats waar wereldmarktleider Forbo jaarlijks honderdduizenden van de klassieke linoleumvloerbedekking onder het merk Marmoleum produceert. Als Product Manager voor linoleum bij Forbo Flooring Systems is Bregje Smulders ook verantwoordelijk voor duurzaamheid - zij legt uit hoe de fabriek relevante milieuveranderingen in de productie heeft geïntroduceerd zodat binnen de productfasen cradle to gate, (A1 tot en met A3), het Marmoleum product klimaatpositief is.
Overal ter wereld geven fabrieken per ton klimaatschadelijke kooldioxide CO2 af aan de lucht; maar in Assendelft is de productie van Marmoleum sinds dit jaar klimaatpositief. Elke vierkante meter Marmoleum haalt 446 gram CO2 uit de lucht, aldus Markus Baum, Technical Product Manager bij Forbo.
Een aantal van onze producten zijn inmiddels nog beter geworden', voegt Smulders toe. Dat is te danken aan de bedrijfsfilosofie - en aan het linoleum zelf. De oorsprong van dit alles ligt in het feit dat to 98% van de grondstoffen voor de Marmoleumvloerbedekking afkomstig is van natuurlijke materialen, waarvan het grootste deel hernieuwbaar is, sommige zelfs als eenjarig gewas. Een duurzame, veerkrachtige vloerbedekking die ecologisch en duurzaam is - 'als linoleum vandaag de dag zou worden geïntroduceerd, zou het waarschijnlijk de uitvinding van de eeuw zijn', aldus Bregje Smulders.
Linoleum bestaat uit natuurlijke grondstoffen. De basis voor deze duurzame vloerbedekking is lijnzaad waarvan de lijnolie wordt gewonnen uit de zaden van de vlasplant. Deze lijnolie wordt gemengd en opgewarmd met boomharsen tot linoleumcement, dat op zijn beurt wordt gemengd met houtmeel en fijngemalen kalksteen en vervolgens wordt gecalandered tot een 2 meter brede jutebrij, die (weer) dient als natuurlijke grondstof voor Marmoleum. Een groot aantal verschillende kleurpigmenten zorgt voor een grote visuele variatie.
De Forbo-fabriek in Assendelft, ten noordwesten van Amsterdam, is de modernste en duurzaamste linoleumfabriek ter wereld. 100 % van de elektriciteit die voor het productieproces wordt gebruikt, is afkomstig van duurzame bronnen zoals wind- en zonne-energie.
Vandaag de dag wordt een groot deel van de productiefasen volautomatisch uitgevoerd. Alleen de grote zwart-wit foto's op de fabrieksmuren, waar nu elektrisch aangedreven heftrucks voorbij komen, getuigen van het handwerk van de beginjaren in Assendelft. De natuurlijke ingrediënten voor het maken van Marmoleum zijn daarentegen niet veel veranderd: linoleum bestaat voor uit lijnolie afkomstig van de zaden van de vlasplant, een snelgroeiend gewas. Alleen al het gewas slaat het grootste deel van broeikasgas op per vierkante meter linoleum. Andere basismaterialen zijn jute en boomharsen, zelf plantaardige grondstoffen, samen met gemalen kalksteenmeel. Aan deze ingrediënten worden houtmeel en gerecycelede resten van de bosbouw toegevoegd. Net als alle andere geupcyclede materialen kunnen deze technisch gezien niet positief worden meegenomen in de ecologische voetafdruk van Marmoleum, maar hebben ze toch hun natuurlijke karakter.
Niet ver binnen de fabriekspoorten bevinden zich de blauwe silo's waarin vrachtwagens uit Noord-Duitsland het houtmeel inpompen. De lijnzaadolie komt per schip door een van de grote grachten die de weilanden tussen Amsterdam en Alkmaar doorkruisen. Forbo heeft sinds 2013 de CO2-uitstoot in haar logistiek met 31,5 % verminderd - zonder de transportroutes te wijzigen. Er zijn milieuvriendelijke bestelwagens aangeschaft en al het verkeer op het fabrieksterrein maakt gebruik van elektrische voertuigen. De weg die de afgewerkte linoleumrollen naar het magazijn afleggen is emissievrij, dankzij een ophangrailsysteem van 750 meter lang. Ook de leveranciers spelen een rol. Vroeger werden conventionele energiebronnen gebruikt om het houtmeel te malen, maar nu gebeurt dit met wind- en zonne-energie. Forbo heeft zelf zonnepanelen geïnstalleerd op de nieuwste van de drie grote magazijnen waarvoor het een LEED-goudkeurmerk heeft gekregen. De productie in de fabriek draait nu al een decennium lang voor 100 % op groene stroom. We hebben hier veel verbeterd', merkt Smulders op bij het beklimmen van de metalen trap naar het gebouw waar lijnolie en boomhars worden verwerkt tot linoleumcement. Het is allemaal een kwestie van de juiste beslissingen nemen. Het linoleumcement borrelt in ketels die bedekt zijn met witte kalk - natuurlijk wordt ook hier groene stroom gebruikt voor het verwarmingsproces. Wat dan in de met kalk bedekte dozen valt, voelt aan als warme kauwgom; sommige stukken zijn bruin, andere meer amberkleurig. Linoleumcement is goed voor circa 1/3 van het eindproduct.
Lijnzaadolie en boomhars worden in grote vaten gekookt - natuurlijk verwarmd met groene stroom. Door oxidatie van de hars en de lijnolie ontstaat linoleumcement: een hete, rubberachtige massa. Om ervoor te zorgen dat dit niet te plakkerig wordt, wordt het gepoederd met kalksteenmeel, een dunne laag die in de hele ruimte wordt afgezet [SB1]. Het linoleumcement wordt vervolgens in opslagplaatsen uitgehard.
Aan de massa wordt kalksteen- en houtmeel toegevoegd dat als vulstof wordt gebruikt, jutevezels als substraat, kleurpigmenten en af en toe de schillen van de cacaobonen om het uitzicht te veranderen. Deze stof wordt later uitgerold op jute banen. Dit proces staat bekend als 'kalanderen'. De vloerbedekking wordt in zijn definitieve vorm geperst over een lange productielijn van walsen en rollers en twee weken lang opgeslagen in droogkamers. Tot slot wordt er een UV-uitgeharde oppervlaktebescherming aan toegevoegd.
De kilometerslange banen worden nu naar de droogkamers getransporteerd. Ervaren specialisten beslissen wanneer ze klaar zijn voor levering. Dit is een wetenschap op zich - en het energie-intensieve deel van de productie. Want de temperaturen in de 20 meter hoge ruimtes zijn sauna-achtig. Zonne-energie is niet genoeg voor dit stadium. We gebruiken nog steeds aardgas', legt Baum uit. Dit kan nog steeds worden verbeterd, de zaken worden ecologischer: in een aantal van de 56 droogkamers zijn meetapparatuur voor het energieverbruik geïnstalleerd.
Hoog gestapeld
Als het eenmaal is geproduceerd, moet het linoleumcement uitharden. Hierdoor komt veel warmte vrij. Hoewel het magazijn onverwarmd is, is de temperatuur hier meestal meer dan 30 graden Celsius, genoeg om andere delen van de fabriek te verwarmen. Net als in de productiehallen worden de speciale kisten voor de uitharding met kalk bestrooid, omdat het hete cement net zo kleverig is als verse kauwgom. Het heeft nu een bruine kleur - soms licht als karamel, soms donkerder, zoals chocolade. Het linoleum krijgt pas later zijn definitieve kleur, wanneer er kleurpigmenten worden toegevoegd.
De afgewerkte Marmoleumbanen worden opgehangen om te drogen. De benodigde warmte wordt opgewekt met behulp van aardgas. Deskundigen beslissen wanneer de Marmoleum uitgehard is - een wetenschap op zich die een grote gevoeligheid vereist.
Zeer verfijnd
Om een gelijkmatige hechting tussen het linoleumcement en de jutebaan te bevorderen, wordt er een laagje granulaat tussen de twee geperst dat voornamelijk bestaat uit gerecycled materiaal. Een vorkheftruck brengt het naar de productiemachine die bekend staat als een 'kalander'.
Helemaal omhoog
Alle voertuigen in de fabriek worden elektrisch verplaatst. De rollen afgewerkt linoleum worden naar het magazijn op 750 meter afstand getransporteerd door middel van een ophangrailtransportsysteem - dat ook op elektriciteit uit hernieuwbare bronnen werkt. Het afgewerkte product zweeft zo hoog boven de hoofden van de werknemers, volledig ecologisch, terwijl het op weg is naar de levering.
Het hele proces wordt verder verbeterd', zegt Smulders. Ze is ervan overtuigd: 'We kunnen het energieverbruik in de toekomst met de helft verminderen. Als het linoleum eindelijk is uitgehard, wordt het op maat getrimd en verpakt voordat het naar het volautomatische magazijn wordt gestuurd. De rollen wachten op de verkoop op gele spindels, waarbij in totaal 110.000 rollen van ongeveer 60 vierkante meter elk hun plaats hebben. Sommige rollen zijn ook afkomstig van een zusterbedrijf in Kirkcaldy, Schotland, de tweede (en originele) linoleumproductielocatie van Forbo. Vanaf hier kunnen we alles gebundeld voor de klant in een enkele zending leveren', zegt Markus Baum, die er nog aan toevoegt: Het is veel efficiënter.
De Schotse rollen bevinden zich in de modernste van de drie magazijnen, die met de zonnepanelen op het dak. Het is bekroond met een 'Leadership in Energy and Environmental Design' (LEED) Certificaat in Goud als een bijzonder milieuvriendelijk gebouw. We willen overal het goede voorbeeld geven', aldus Bregje Smulders. Vanuit de hal, die eruitziet als een grote groene kubus, kan men omhoog kijken naar de oude schoorsteen aan het einde van het enorme fabrieksterrein. We willen een stempel drukken', merkt Smulders op. Het herkenningspunt van de oude industrie, genesteld tussen de weilanden en grachten langs de N8, heeft nu gezelschap.
Linoleum kan niet alleen gebruikt worden om hoogwaardige vloeren te realiseren, maar ook als materiaal voor meubels, kasten, deuren en scheidingswanden. Er is ook een prikbord linoleum genaamd bulletin board dat zachter en geluidsabsorberend is, vaak gebruikt als een klassiek prikbord paneel of als wandbekleding. De afdeling Forbo Development doet voortdurend onderzoek naar innovatieve kleuren, vormen en ontwerpen.
Tekst: Robert Otto-Moog / Fotograaf: Matthias Groppe, Paderborn