Conveyor belts for baggage handling
Flawless baggage handling logistics keep your airport efficient and customers happy. And that’s where our high-quality, energy-efficient conveyor belts come in.
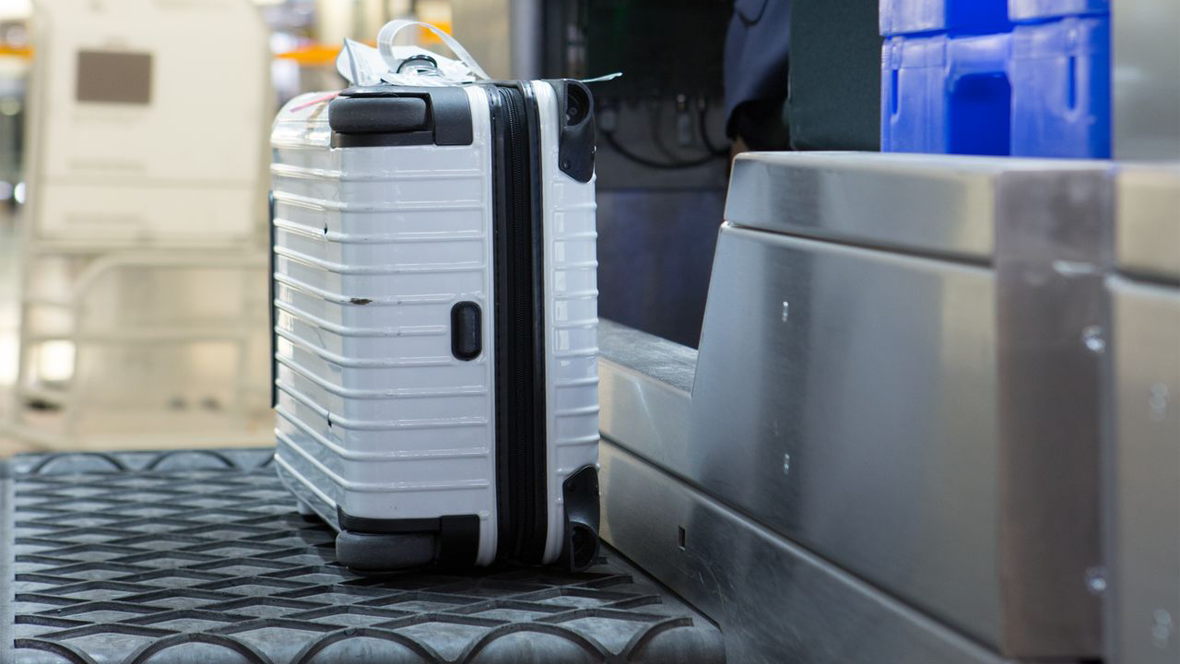
From check-in to security screening to loading and unloading, you need the right belt to run an airport efficiently. In exactly the quality you expect. All our belts comply with airports’ stringent demands. They are flame retardant, impact resistant, antistatic, low noise, track consistently, and operate at high and low temperatures. We’re constantly investing in innovative, new solutions.
„In addition to efficiency, sustainability is becoming ever more important. Airports have to achieve climate goals, such as carbon neutrality, which are specified by shareholders and politicians. Our conveyor belts offer airports, airport operators and systems integrators the energy-saving potential demanded. What’s more, some of the conveyor belts in our portfolio are made from recycled PET bottles. Improve your environmental footprint and cut your running costs too. As an expert in baggage handling logistics in airports, I can help you achieve your sustainability goals with Forbo products.“
„Forbo Movement Systems belts are some of the market’s top-performing products. We’ve successfully fitted out hundreds of airports worldwide, as our satisfied customers and partners can confirm. But we don’t stop there. We’re investing in innovations to make better products all the time. For instance, more energy-efficient, robust, low-noise belts made of recycled material. To ensure your airport runs efficiently and sustainably.“
Amp Miser is Forbo Movement Systems’ conveyor belt that verifiably generates energy savings of up to 50%.
Our Amp Miser belts have been certified by German inspection body TÜV Rheinland and presented with the Best of Industry Award 2023 in the Best Sustainability Project category. Where goods are conveyed continuously and lots of belts are used, as in airports, the savings are very apparent and ensure a fast return on investment. Which is why lots of airports are harnessing Amp Miser’s energy-saving potentials.
Get to know Amp Miser
Forbo Movement Systems is a long-standing member of the GATE Alliance, the airport industry’s leading network. We collaborate with them to develop the concepts and technologies of tomorrow, particularly in terms of sustainability and energy efficiency.
www.gate-alliance.com
As a member of the International Association of Baggage System Companies (IABSC), Forbo Movement Systems campaigns for consistent improvement of standards and innovations in the baggage handling industry.
iabsc.org
In the white paper "Saving energy operating baggage handling systems", we examine the energy consumption of belt conveyors. Measurements in the laboratory and on active airport systems prove this: By using appropriate conveyor belt types, energy savings of over 40% can be achieved for the entire conveyor. Amortisation calculations show that possible additional costs are more than compensated for by lower energy costs. Secondary effects such as longer belt service life and longer conveying distances with an identical drive can further reduce the overall costs of the system.
To the whitepaper
In addition to the energy savings of our Amp Miser belts in general, these belt types offer an additional sustainability benefit. Their tension member fabric is made from 100% recycled PET bottles (ECOFIBER). Valuable raw materials are saved during production without compromising on quality and service life. At the same time, energy consumption and therefore CO2 emissions are significantly lower during production.
to the ecofiber page
Forbo Movement Systems is equipping Schiphol Airport with conveyor belts. Together with the supplier of the baggage handling systems, we are working on reducing the energy consumption of the baggage handling system by using energy-efficient belts. The Winning Solution describes the project of introducing Amp Miser and measuring the savings potential.
To the Winning Solution
Our multi-layer, fabric-based, Siegling Transilon and Siegling Transtex conveyor belts are destined for diverse conveyor and processing tasks. In all areas of the baggage handling, they are real all-rounders, or customized for specific applications such as tray conveying.
Special belts for curves are flexible in all directions – both horizontally and spirally – and can easily handle even complex requirements.
Conveyor belts for the infeed and outfeed merging of items of baggage fulfill one of the core tasks of baggage handling systems. Conveyor belts from Forbo Movement Systems are highly accepted in this industry.
The Amp Miser conveyor belts meet all standards. They are robust, flame retardant, antistatic, low noise and operate in the temperature range required. And they are verifiably energy efficient. Thanks to the low friction coefficient, Amp Miser enables smaller motor gearbox sizes, longer conveyors and a reduction in the number of motors.
With recycled PET in the tension members, the Transilon ECOFIBER belts save on primary raw materials and therefore help you to reach your sustainability goals.
To the Amp Miser conveyor belts
To the ECOFIBER conveyor belts
The Siegling Prolink plastic modular belts are robust and durable. They enable efficient conveying and processing, which is often not possible with conventional belting material. Diverse materials, shapes, pitches, patterns, and open areas provide all sorts of options in airport logistics processes.
To the Siegling Prolink conveyor belts
Our experts can tell you anything you want to know about conveyor belts at airports.
To the contact form