Linoleum Nett Fit Seams
Technical Talk Series with Craig Thornhill, Technical Services Manager
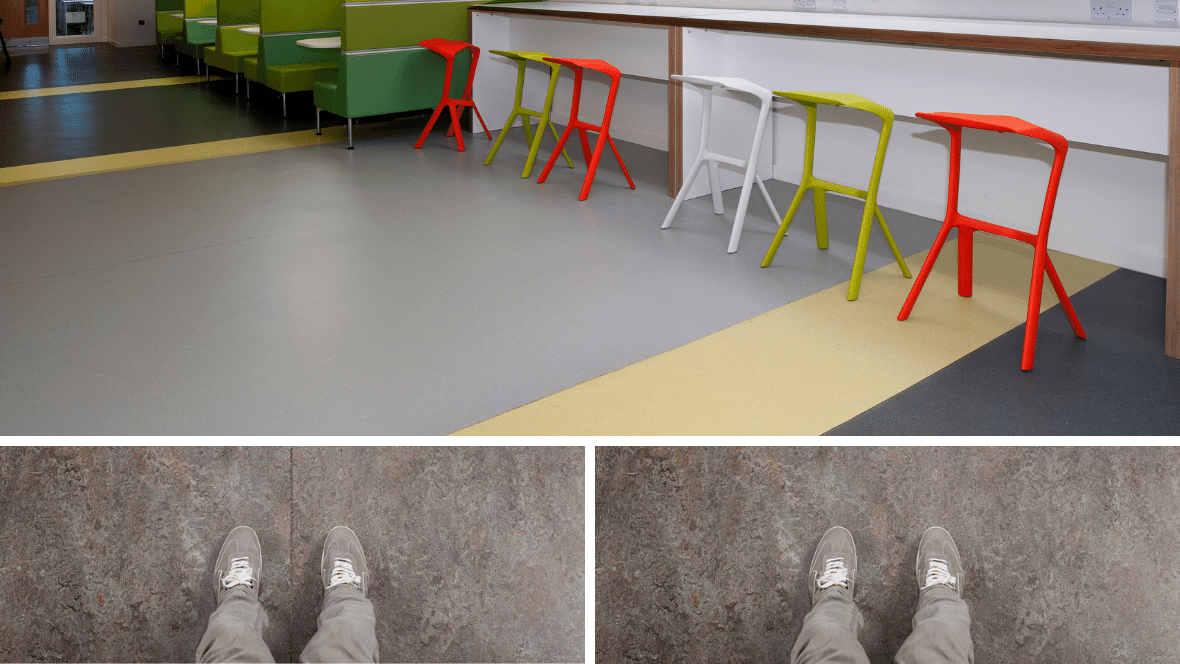
This Tech Talk starts with an insight into the linage of linoleum - it is a fascinating product and its history is sometimes overlooked. This sets the background about seams in linoleum as there is some widespread misunderstanding about what you can achieve without welding. You can simply cut a seam so that the two widths of material closely abut to form what is also knows as ‘nett fit seam’. This is an important alternative fitting option not only because welding costs time and money but in many cases the appearance of a nett fit seam is aesthetically superior.
Linoleum has been around for many years. In fact, the product was first invented back in 1860 by Sir Frederick Walton who initially intended it for use as a ship deck covering (hence the term ‘Battleship Linoleum’). The probable origin of this product was in the 1700s when non-woven floor coverings were made of oil cloth – a heavy canvas coated with wax or oils (for water resistance and durability) that were then painted for decoration. I was raised in a Victorian house and remember the multi-coloured/patterned flooring in the hall and my great aunt mentioning ‘oil cloth’.
The invention of linoleum – patented in 1863 by Sir Walton – had a revolutionary impact as it was the first modern floor covering. From the late 19th century right up until the 1950s, it was one of the few products which was simultaneously practical, hardwearing, non-flammable, low-maintenance and cheap.
Because of its durability and ease of production, Sir Walton's linoleum quickly found use as a floor covering in buildings - a much larger application than battleships. Linoleum's appeal arose from its properties as a durable, water-resistant sheet floor covering. With a backing of jute or canvas to resist cracks and tears, this flooring has enjoyed a long history of durability and service.
After 1877, when Sir Walton's patent expired, production became more widespread in Britain and abroad, spreading in particular to Scotland and to the town of Kirkcaldy in West Fife. Kirkcaldy had established itself as the world's largest centre for the manufacture of wax floor-cloth and was in an ideal position to exploit a rapidly growing national and international market for linoleum. Today only the Forbo Flooring linoleum manufacturing plant remains in Kirkcaldy, enjoying over 150 years of production.
For the vast majority of these years, linoleum has been successfully fitted as a sheet material without the need to weld the seams. In fact, welding was not deemed necessary and therefore not available until the advent of sheet vinyl flooring (these ‘new’ vinyl products needed to be seam welded as the dimensional stability was less than perfect) introduced the concept.
Unlike vinyl sheet, linoleum is produced using natural raw ingredients and, as such, has very different performance characteristics. One of these is the way in which the seams (joins between individual sheet pieces) in linoleum work. It is important to understand that whether seams are to be welded or not, they should always be cut to leave a nett fit (closed) seam. Linoleum, in common with sheet vinyl, should not be ‘gapped’ at seams to ‘help facilitate grooving and welding’, as is often seen on sites.
It is critical that when cutting seams in linoleum sheet, an allowance is made for a fractional expansion in the width of the hessian backed material as it picks up moisture from the adhesive before it dries. This expansion is minute and will be halted by the curing of the special linoleum adhesive (linoleum adhesive is a hard-set adhesive which, when dried, prevents any movement in the linoleum sheet and provides a water-resistant bond).
Unless allowed for in trimming/cutting, tightly cut seams will peak (curl at edges) and fail – it is important to point out that this is product characteristic not a product defect as it can be controlled at the fitting stage.
So, nett fit seams are not a new phenomenon but something that has long historical roots and credibility. A correctly cut seam (with a slight undercut) will close during the curing of the adhesive and will not open up during the life of the linoleum. Nett fit seams are often considered to be aesthetically better than welded seams, so if the installer possesses the skills to achieve a good seam and, if the application allows, welding of linoleum is not obligatory.
This is particularly relevant in the case of plain colour linoleums. Forbo Flooring recommends that plain colour linoleum is aesthetically best fitted with nett fit seams unless the application determines that welded seams are required.
Nett Fit Seam
Welded seam using multi-coloured matching welding rod
Immediately after fitting and rolling the sheet pieces, trace the seam with recess scribers or trimmer along the trimmed edge of the first sheet (linoleum should be fitted and rolled one sheet piece at a time to minimise any sideways seam movement) and cut through with a utility knife and hooked blade, again with a slight undercut.
Once the seam is cut, the cut edge should just fall into place alongside the edge of the first sheet (if the sheet needs to be pushed against the previously stuck sheet the seam is too tight and will peak).
It is important to cut and roll the seam whilst the adhesive is still wet to ensure full adhesion and avoid the potential for peaking seams. Remove any adhesive residues at the seam straight away with a damp cloth.
Tip: If the guide on your recess scribers is too thick (Fig. a) it could remove adhesive from the subfloor when scribing the seam. Sanding the bottom of the guide on the recess scriber to reduce its thickness (Fig. b) will prevent this and will also help to keep the guide clean and free of adhesive contamination.
Tip: check the quality of the nett fit seam on completion. If there are any small, isolated gaps in the length of the finished seam these may be filled using the following technique:
• Clean the area of the repair paying attention to the removal of any loose linoleum fragments or dust.
• Make up a paste by mixing fine shavings, ground or sanded to make a fine dust, from a piece of the original colour linoleum with a waterproof PVA adhesive.
• Fill the area to be repaired with the paste using an appropriate tool such as a spatula, leaving the filler flush with the surface of the linoleum.
• Remove any excess with a damp cloth.
• Smooth the finished repair with a spatula and allow to dry.
• When the filler is completely dry, buff the surface to an even finish, applying a thin coat of diluted floor maintainer if required.
Tip: If applying floor maintainer use a small brush or similar to the filler only, thereby avoiding gloss variations in the flooring adjacent to the filler.
Sheets pushed against each other will cause the seam to peak
Sanded scriber guide to help prevent removal of adhesive
If welded seams are required, then the seams for welding should be formed in the same manner as a nett fit seam is still required.
One concern over the use of nett fit seams is that the seam will allow water to penetrate and cause the installation to fail. This is not the case with correctly fitted linoleum and nett fit seams.
At Forbo Flooring, we demonstrate the robustness of the nett fit seam by floating plastic ducks in a purpose built ‘tank’ and leaving them for several days. The only loss of water is through evaporation! This is a fun way to also show that linoleum is a water-resistant floor finish which can be easily compared in performance to sheet vinyl floorings.
Note: The procedures and actions described above are suggested to assist in resolution of minor installation related problems. They do not form part of any official installation recommendation, and manufacturers cannot take responsibility for the long-term effectiveness of any such repairs or warrant the repaired areas. As with any repair, the quality and effectiveness of the work, which includes visual acceptability, will depend on the skill of the operator. The final acceptance of any repair is at the sole discretion of the client/end user.