Closing the loop
Dealing with used flooring and product waste responsibly is the final step to creating a circular model for flooring. We have devised various strategies for dealing with waste to reuse as many materials as possible and minimise what goes to landfill.
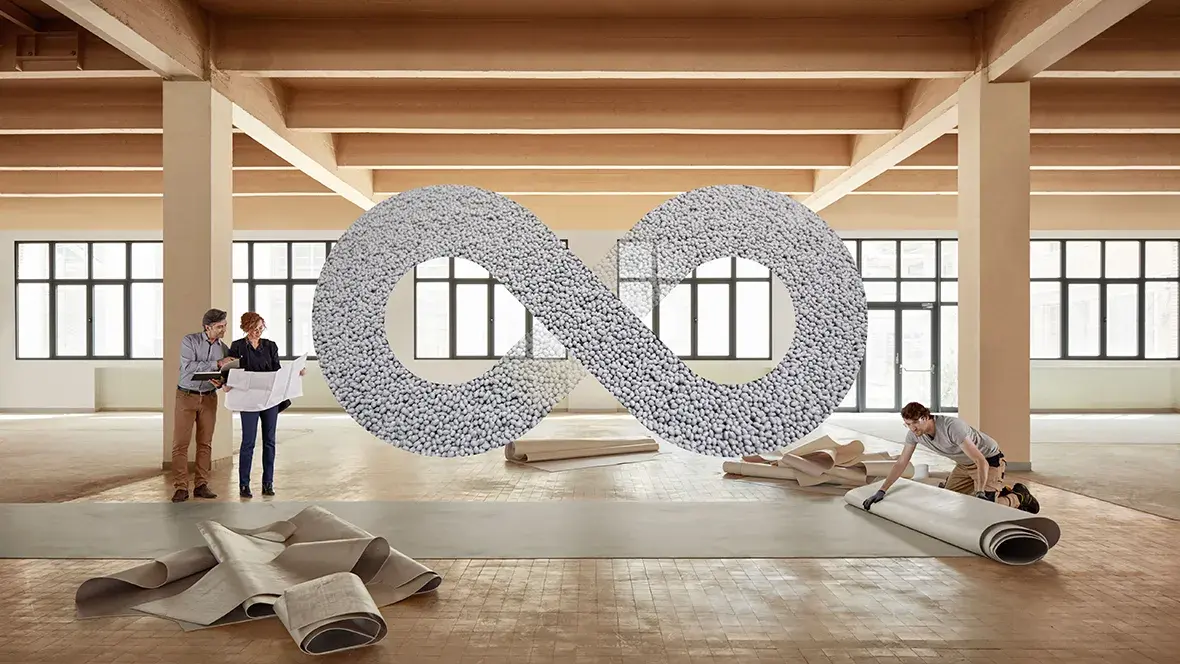