Nuestro linóleo es bueno por naturaleza.
Captura más CO2 del que libera, si se fabrica del modo adecuado, tal como hace Forbo.
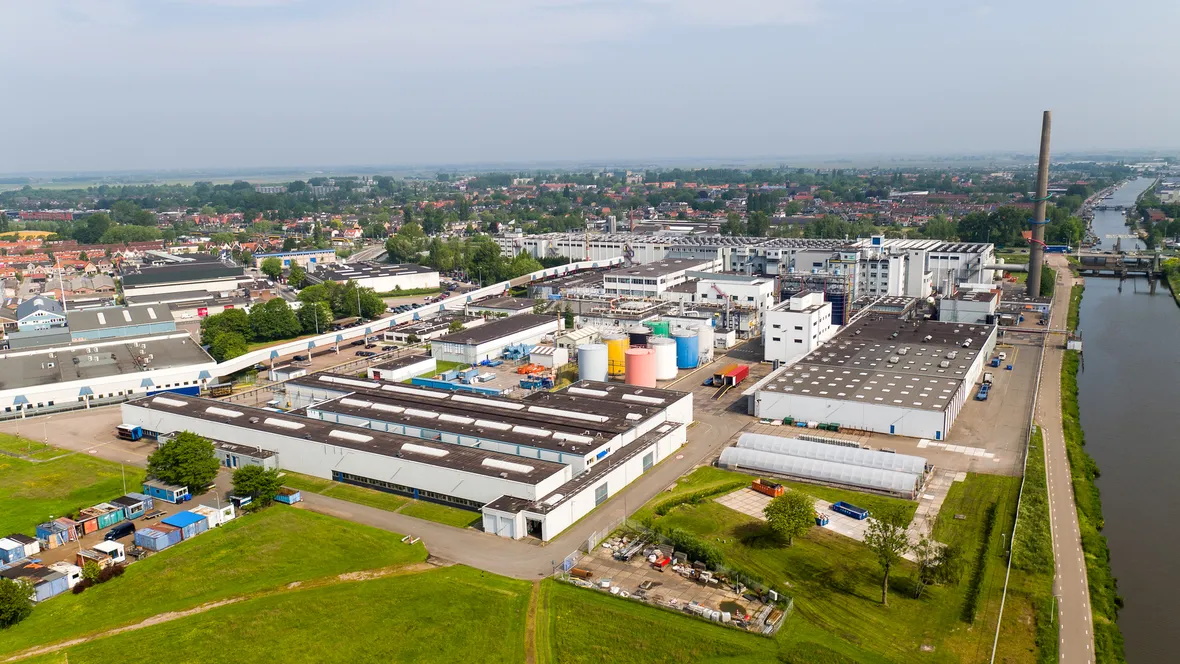
Cualquiera que conduzca desde Ámsterdam hacia Alkmaar verá principalmente prados y canales. Esto hace que los elegantes anillos de colores alrededor de la chimenea en desuso de la fábrica, cerca de la salida de la autopista Assendelft, resulten todavía más llamativos. "Realmente es una especie de hito", afirma Bregje Smulders. "Incluso si en realidad nunca se llegó a utilizar". La fábrica de linóleo, la más grande y moderna del mundo, a poco menos de media hora en coche al noroeste de Ámsterdam, es donde Forbo produce cientos de miles de pavimentos de linóleo todos los años bajo su marca Marmoleum. Como Gerente de Producto para linóleo en Forbo Flooring Systems, Bregje Smulders también es responsable de la sostenibilidad. Ella explica cómo la planta introdujo cambios medioambientales importantes en la producción para que, dentro de las fases del producto desde la cuna hasta la puerta, (A1 hasta A3 incluido), el Marmoleum presentara unas emisiones neutras de CO2.
En todo el mundo, las fábricas liberan al aire toneladas de dióxido de carbono (CO2) perjudicial para el clima; pero en Assendelft, la producción de Marmoleum es completamente neutra en emisiones de CO2 desde principios de 2018. 'En realidad, si lo calculas, desde este año lo hacemos incluso mejor que eso; cada metro cuadrado de Marmoleum que fabricamos realmente libera al medio ambiente de más de 400 gramos de dióxido de carbono', dice Markus Baum, Director Técnico de Producto de Forbo.
Algunos de nuestros productos incluso han mejorado un poco más", añade Smulders. Este hecho se debe a la filosofía de la empresa y al propio linóleo. El origen de todo radica en que hasta el 98% de los componentes del pavimento Marmoleum proceden de materiales naturales, de los cuales la mayoría son renovables, algunos incluso rápidamente renovables como cultivos anuales. Un pavimento duradero, resiliente, ecológico y sostenible: "si el linóleo se introdujera hoy en día, probablemente sería el invento del siglo", señala Bregje Smulders.
El linóleo se compone de materias primas naturales. La base de este pavimento sostenible son las semillas de lino, cuyo aceite se extrae de las semillas de la planta del lino. Este aceite de linaza se mezcla y se calienta con colofonia de árbol para fabricar cemento de linóleo, que a su vez se mezcla con harina de madera y piedra caliza finamente molida y luego se calandra sobre una masa de yute de 2 metros de ancho, que sirve de (de nuevo) capa de soporte de material natural para el Marmoleum. Una serie de pigmentos de colores diferentes garantiza una gran variedad visual.
La fábrica de Forbo en Assendelft, al noroeste de Ámsterdam, Países Bajos, es la fábrica de linóleo más moderna y sostenible del mundo. El 100 por cien de la electricidad utilizada para el proceso de producción proviene de fuentes renovables como las fuentes de energía eólica y solar.
En la actualidad, una gran parte de las fases de producción se realiza de forma totalmente automática. En la actualidad, sólo los grandes cuadros en blanco y negro de las paredes de la fábrica, por donde ahora pasan apresuradamente carretillas elevadoras accionadas eléctricamente, dan testimonio del trabajo manual de los primeros años en Assendelft. Los ingredientes naturales del Marmoleum, por otra parte, no han cambiado mucho: el linóleo se compone de aceite de linaza derivado de las semillas de la planta del lino, un cultivo de rápido crecimiento. El lino almacena por sí solo la mayor parte de los gases de efecto invernadero del linóleo. Otros materiales básicos son el yute y las colofonias de árbol, materias primas también vegetales, junto con harina de piedra caliza molida. A estos ingredientes se añade la harina de madera, residuos reciclados de la producción forestal. Como todos los demás materiales reciclados, técnicamente no pueden incluirse positivamente en la huella medioambiental del Marmoleum, pero siguen teniendo su carácter natural.
Ubicados cerca de las puertas de la fábrica, se encuentran los silos azules en los que los camiones del norte de Alemania bombean la harina de madera. El aceite de linaza llega por barco a través de uno de los grandes canales que cruzan los prados entre Ámsterdam y Alkmaar. Forbo ha reducido las emisiones de CO2 en su logística en un 31,5% desde el 2013, sin cambiar las rutas de transporte. Se han comprado camionetas ecológicas, y todo el tráfico en los terrenos de la fábrica se realiza con vehículos eléctricos. El camino que toman los rollos de linóleo terminado hasta el almacén está libre de emisiones, gracias a un sistema de cinta transportadoras con rieles de suspensión de 750 metros de largo. Los proveedores también juegan un papal importante. Antiguamente se utilizaban fuentes de energía convencionales para moler la harina de madera, pero ahora se hace con energía eólica y solar. Forbo ha instalado paneles solares en uno de los tres grandes almacenes (el más nuevo) para el que recibió una certificación LEED Gold. Hace ya una década que la producción en la fábrica funciona al 100% con electricidad verde. "Hemos mejorado mucho aquí", comenta Smulders mientras subimos los escalones de metal que nos conducen al edificio donde se procesan el aceite de linaza y la resina para crear el cemento de linóleo. "Se trata de tomar las decisiones correctas". El cemento de linóleo burbujea en las calderas cubiertas con cal blanca. Naturalmente, aquí también se usa electricidad verde para el proceso de calentamiento. Lo que más tarde cae en las cajas cubiertas de cal parece un chicle tibio; algunas piezas son marrones, otras de color ámbar. El cemento de linóleo representa alrededor de un tercio del producto posterior.
El aceite de linaza y la resina se hierven en grandes recipientes, naturalmente calentados con electricidad verde. La oxidación de la resina y del aceite de linaza produce el cemento de linóleo: una masa caliente parecida al caucho. Para evitar que este material no se vuelva demasiado pegajoso, se pulveriza con harina de piedra caliza, una capa delgada que se deposita en todo el espacio. Posteriormente, el cemento de linóleo se cura en almacenes de gran altura.
A la sustancia resultante se le agrega la harina de madera y la piedra caliza, que se utilizan como relleno, las fibras de yute como sustrato, los pigmentos de color y, ocasionalmente, las cáscaras de los granos de cacao. Posteriormente, esta sustancia se extiende sobre correas hechas de fibras de yute. Este proceso se conoce como "calandrado". El pavimento se presiona entonces para darle su forma final sobre una larga línea de producción formada por ruedas y rodillos, y se almacena en las salas de secado durante dos semanas. Finalmente se aplica una protección de superficie curada con UV.
Los rollos de un kilómetro de largo se transportan a las salas de secado. Los especialistas experimentados deciden cuándo están listos para la entrega. Esta es una ciencia en sí misma, y la fase de producción que más energía consume, porque las temperaturas en las salas de 20 metros de altura son similares a las de una sauna. La energía solar no es suficiente para esta fase. "Seguimos utilizando gas natural", explica Baum. Esto aún puede mejorar, y nos estamos preparando para ser más ecológicos: se han instalado dispositivos para medir el consumo de energía en algunas de las 56 salas de secado.
Una vez producido, el cemento de linóleo necesita curarse. Esto libera una gran cantidad de calor. Aunque el almacén no tiene calefacción, la temperatura aquí suele superar los 30 grados centígrados, suficiente para calentar otras áreas de la fábrica. Al igual que las salas de producción, las cajas especiales para la curación están espolvoreadas con cal, porque el cemento caliente es tan pegajoso como un chicle. En esta fase tiene un color marronoso, a veces claro como el caramelo, a veces más oscuro, como el chocolate. El linóleo no recibe su color final hasta más tarde, cuando se agregan los pigmentos de color.
Los rollos de Marmoleum se cuelgan para que se sequen. El calor requerido se genera utilizando gas natural. Los expertos deciden cuándo el Marmoleum está listo, toda una ciencia en sí misma que requiere mucha sensibilidad.
Para fomentar una adhesión uniforme entre el cemento de linóleo y el revés de yute, se inserta entre los dos una capa de granulado que consiste principalmente en materiales reciclados. Con una carretilla elevadora se lleva hasta la máquina de producción conocida como "calandria".
En la fábrica, todos los vehículos se mueven eléctricamente. Los rollos de linóleo terminado se transportan al almacén, que está a 750 metros de distancia, mediante un sistema de cinta transportadora con rieles de suspensión, que también funciona con electricidad de fuentes renovables. Así pues, el producto terminado, cuelga por encima de las cabezas de los empleados, de manera completamente ecológica, a medida que avanza hacia la entrega.
"Seguiremos mejorando aún más todo el proceso", afirma Smulders. Está convencida: "Podríamos reducir el consumo futuro de energía a la mitad". Una vez curado el linóleo, se corta a medida y se empaqueta antes de enviarlo al almacén, que está totalmente automatizado. Los rollos esperan su venta en husillos amarillos, con un total de 110.000 rollos, que miden alrededor de 60 metros cuadrados. Algunos de ellos también provienen de una fábrica hermana en Kirkcaldy, Escocia, la segunda (y original) fábrica de linóleo de Forbo. "Desde aquí, podemos entregar todo lo que se incluye al cliente en un solo envío", dice Markus Baum, y agrega: "Es mucho más eficiente".
Los rollos procedentes de la fábrica de Escocia se guardan en el almacén más moderno de los tres, el que tiene paneles solares en el techo. Este almacén ha recibido Certificado LEED Gold (Liderazgo en Energía y Diseño Ambiental) por tratarse de un edificio especialmente respetuoso con el medio ambiente. "Queremos liderar con el ejemplo en todas partes", señala Bregje Smulders. Desde el vestíbulo, que parece un gran cubo verde, se puede ver la vieja chimenea en el extremo más alejado de los enormes terrenos de la fábrica. "Queremos dejar una marca", señala Smulders. El hito de la antigua industria enclavada entre los prados y canales a lo largo de la autopista N8 ahora tiene compañía.
El linóleo no solo se puede utilizar para fabricar pavimentos de alta calidad, sino también como material de revestimiento para mobiliario, armarios, puertas y paneles de separación. También se puede utilizar como tablón de anuncios, como la colección Bulletin Board que es más blanda y absorbe el ruido. El Departamento de Desarrollo de Forbo está constantemente buscando la creación de colores, formas y diseños innovadores.
Texto: Robert Otto-Moog / Fotógrafo: Matthias Groppe, Paderborn