Forbo recycling in practice
At Forbo Flooring Systems, we are committed to transforming all our linear processes and products so they support the circular economy. Read more on how recycling at Forbo Flooring Systems is done in practice.
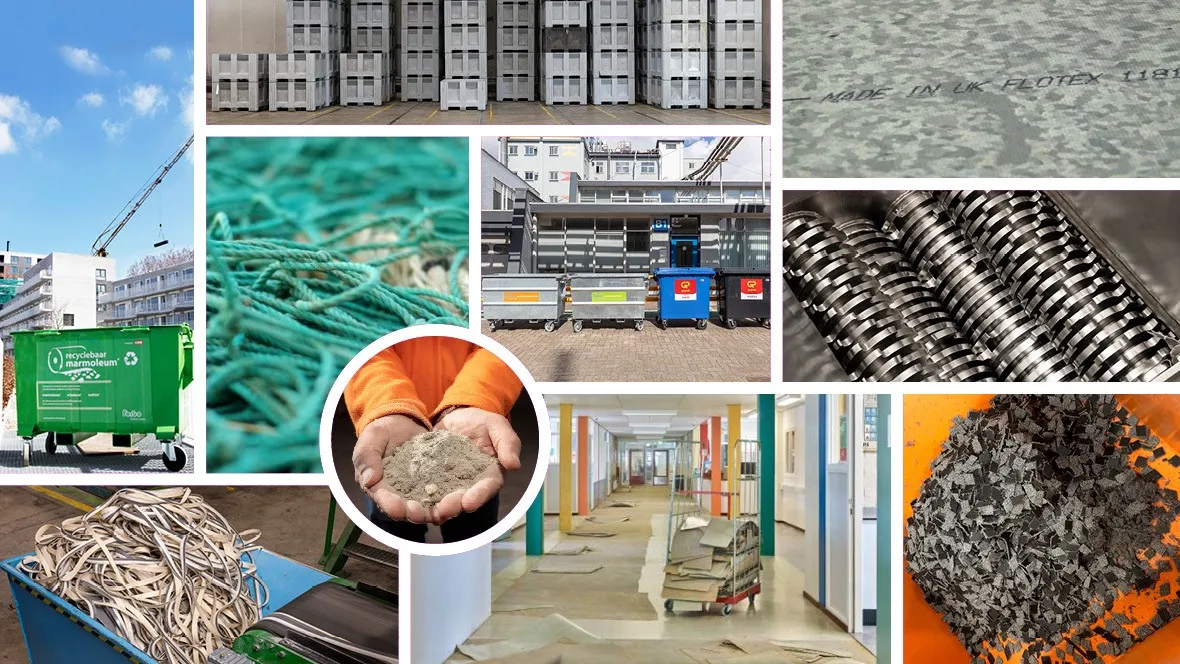
The essence of a circular economy is to preserve natural resources by retaining the quality and value of products and their parts. At Forbo Flooring Systems, we believe that biobased solutions create a better future for our planet. But when biobased is not an option, circularity provides the next best alternative – as long as the life cycle impact is measurably better.
The circular economy requires us to transform our thinking. This starts in the design phase of our products and covers sourcing more sustainable raw materials, efficient use of energy and ways to reduce waste as part of the initial product design concept.
We are using resources more efficiently by changing the way we think about products and production processes. Is the product the best way to meet the demand? Could we use fewer or different resources in its production? And when it comes to designing differently, which reuse, repair and recycling options should we consider in advance of production?
All our factories have an ISO 14001 certification, which has become the international standard for designing and implementing an environmental management system. It applies to the environmental aspects of our activities, products and services that we can control or influence considering a life cycle perspective.
To give you a better idea, here are some of the ways that we collect, process and re-use materials in our factories today:
Forbo Flooring in Assendelft develops, produces and markets linoleum floor coverings, bulletin boards and finishing material for (office) furniture. Our factory in Kirkcaldy develops and produces linoleum floor coverings like Marmoleum Modular.
Marmoleum, our linoleum brand, is a true environmental evergreen. Made from natural raw materials and produced in a modern and efficient production environment running on green electricity, the production of this floor covering is actually carbon negative from cradle to gate.
In our linoleum factories, the vast majority of linoleum waste is being re-used in Marmoleum products. Other valuable streams, like jute or furniture linoleum backing paper residuals are offered to parties that upcycle them into highly valuable or socially responsible products. Installation residues are also collected and added to the recycling system on our sites, contributing to the 43% recycled content in Marmoleum.
'For as long as I can remember, we have worked with the 4 R principle of reduce, renewable, reuse and recycle, which today in a popular way is expressed in the circular economy model. Having a broad portfolio of product solutions and using a large amount of natural renewable raw materials give us an advantage in progressing towards circularity, but it is clear that we cannot do this on our own. We need to work together as an industry and as producers.'
Jean-Michel Wins, Executive Vice President of Forbo Flooring Systems
Forbo’s vinyl portfolio represents state-of-the-art quality and is manufactured in ultra-modern and energy-efficient production plants. Forbo Flooring in Coevorden produces and develops resilient flooring for applications in residential and commercial areas, like Novilon, Novilux, Step, Eternal and Allura.
Forbo Sarlino in Reims is developing and producing acoustic project vinyl and needlefelt floor coverings. Our factory in Giubiasco specialises in the production of homogeneous vinyl tiles such as Allura Colour, and is worldwide a key supplier of ESD floor coverings, such as Colorex Plus and Colorex SD/EC.
Vinyl floor coverings are part of a versatile range of products whose technical and sustainable properties have, over the years, undergone a metamorphosis. Apart from improving recycled or reused content, further advances have been made in lacquers and dyes, which are waterborne, nowadays, while product emissions have been reduced to near zero and harmful substances eliminated. We offer a commercial portfolio of fully phthalate-free vinyl.
Forbo Flooring Coral in Krommenie is the factory where we produce the Coral entrance products. Well-designed entrance floors not only offer a sustainable solution in and of themselves, they also contribute to the sustainability of the building in which they are used, throughout the life cycle of that building.
Our entrance floor covering can stop up to 95% of dirt from being walked into the building. In this way, entrance flooring can protect the quality of an interior, lengthen the use of a floor and cut down on cleaning and maintenance costs and the use of detergents. We use yarns that are upcycled from old fishing nets for a large number of our Coral collections. The primary backing of our Coral Welcome entrance flooring is made from recycled PET bottles.
Our tufted carpet tiles collection Tessera, the largest manufactured collection on one site in the world, is produced in Bamber Bridge. With high-end infinity machines we are able to develop and produce specialized carpet tiles which are not easy to make.
With a minimum recycled content by weight of 57% our Tessera carpet tiles have the highest recycled content in the industry. Some of our ranges, for example Create Space 1, even have a recycled content by weight of 70%.
During floor design, we create random lay tiles so that the parts of the floor that see heavy use can be replaced without this impacting the overall design. We are also experimenting with end-of-life solutions, especially those that involve separating the tiles’ textile layer from their backing.
In our factory in Ripley we produce Flotex sheet and tiles. In 2001 we almost completely eliminated our use of landfill by installing the first recycling plant of its kind to convert pre-consumer waste into high performance carpet tile backing. Today this facility processes nearly 50 tonnes of waste a week.
In our factory in Chateau Renault we produce our special Flotex Vision and the designer collection Flotex Sottsass. Our factory in Chateau Renault holds two digital printers which print bespoke designs on white Flotex sheet.
Forbo’s Flotex collections are different from conventional sheet and tile textile floor coverings. They are created from 6.6 nylon fibres with an impervious backing that create a dense, comfortable surface that is sturdy and resilient as well. Flotex is available in sheet, planks and tiles. The modular solutions contain a high percentage of recycled material.
Circularity continues to play a big role in our sustainability goals for the future. We want to keep contributing to the circular economy by increasing the recyclability of the products that we sell and by making sure that all products contain as much recycled content as possible.
Of course, it doesn't stop there. Post-consumer waste, for example, is a greater challenge for the industry as such in terms of collection and transport as well as the selection and processing. To be ready for that achievement we now for example offer loose-lay solutions that enable ‘clean’ post-consumer recycling.
Want to know more about our efforts? Read all about our Sustainability Program 2025 and our circularity goals for the next five years:
OUR SUSTAINABILITY PROGRAM FOR 2025